Optimierung der Logistik im Ersatzteillager – Sechs erprobte Ansätze
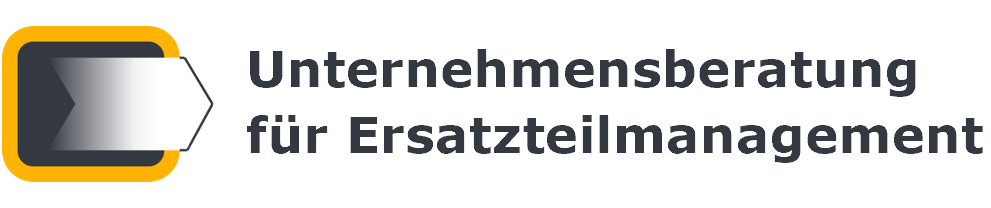
Oft sind die Lagerstrukturen gewachsen, die Prozesse vom Produktionslager übernommen.
Aber die Ersatzteillogistik "tickt" doch anders
Daher bieten die meisten Ersatzteilläger viel Raum zur Optimierung ihrer Logistikprozesse
Ersatzteillager konsequent am Kunden ausrichten:
jedes Lager ist anders
Das eine Erfolgsrezept gibt es nicht. Denn die Anforderungen der Kunden sind von Branche zu Branche verschieden. Außerdem erfordert die Belieferung nach Australien andere Voraussetzungen als die an einen deutschen Service-Techniker.
Hinzu kommen die sehr unterschiedlichen Anforderungen aus
- Gängigkeit,
- Größe,
- Mengen,
- physischen Eigenschaften
der Ersatzteile.
Außerdem ist es entscheidend, zu verstehen, was der Kunde wirklich will. Überlegen Sie, was Ihr eigentliches Produkt sein soll:
Wollen Sie Teile verkaufen?
Dann sind Sie austauschbar. Und zudem über den Preis vergleichbar.
oder
Wollen Sie nicht eigentlich Zeit verkaufen?
Das kann zum Beispiel reduzierte Stillstandszeit sein. Oder auch Prozesszeit bei Ihren Kunden. Dann müssen Sie Ihr Lager auch an der Durchlaufzeit messen.
Denn was hilft die beste Verfügbarkeit Ihrer Teile, wenn Sie diese nicht umgehend ausliefern?
Orientieren Sie sich dabei an Amazon. Und messen Sie, wie oft Ihr Ersatzteillager Ihre Kunden eben nicht taggleich beliefert hat. Die Optimierung eines Ersatzteillagers ist jedenfalls nicht, dass Sie 95 % Lieferzuverlässigkeit erreicht haben. Sondern vielmehr, was die fehlenden 5 % ausmachen. Denn hier werden Sie mit Beschwerden rechnen müssen.
Insofern ist Ihr Ersatzteillager nur ein Glied in der Kette Ihrer Ersatzteillogistik. Und nur die optimale Kraftübertragung der gesamten Kette bringt Ihnen die erforderliche Kundenzufriedenheit.
1. Kennzahlen nutzen zur Optimierung aller Logistikprozesse Ihres Ersatzteillagers
Natürlich können Sie oft eine Fülle von Maßnahmen schon durch kritische Betrachtung finden. Doch in der Regel reicht das nicht.
Manchmal liefert ein ERP oder ein Lagerverwaltungssystem (LVS) erste aussagefähige Kennzahlen. Diese, als Dashboard verarbeitet, helfen oft, Tendenzen zu erkennen. Ob die Werte allerdings "gut" sind im Sinne einer Optimierung, sagt Ihnen nur der Vergleich mit anderen Ersatzteillägern.
Darüber hinaus reichen die im Standard vorhandenen Kennzahlen in den seltensten Fällen. Die Logistikprozesse gerade in Ersatzteillägern sind so vielfältig, dass mehr Transparenz der Daten notwendig wird. Allerdings bieten in Zeiten der Digitalisierung die meisten Systeme Möglichkeiten des Daten-Downloads. Aus solchen Massendaten können Sie mit vorhandenen Mitteln, wie Excel oder Access, schnell Kennzahlen bilden. Denn tausende Datensätze alleine erlauben schließlich noch lange nicht die gewünschte Transparenz.
Diese Informationen bilden dann die Grundlage zur Optimierung Ihrer Logistikprozesse. Und außerdem zur Reduzierung Ihrer Lagerkosten.
Damit wird die Basis geschaffen, um Zusammenhänge zu erkennen. Außerdem erlauben Kennzahlen Ihnen eine Priorisierung von Maßnahmen im Rahmen einer Optimierung der Logistikprozesse im Ersatzteillager.
Bestandsanalyse für Optimierung der Logistikprozesse im Ersatzteillager
Saubere Daten als Basis jeder Optimierung eines Lagers
Eigentlich ist es eine Selbstverständlichkeit. Nämlich, dass die Bestände stimmen. Gleiches gilt für die speziell in den Logistikprozessen eines Ersatzteillagers erforderlichen Stammdaten, wie
- Gewicht (erforderlich für Zoll und Maximal-Lasten in Regalen),
- Vorzugslagerbereich,
- Gängigkeit,
- Fassungsvermögen in Behältern / Fächern,
- Maximal-Gewicht pro Fach / Regal-Ebene,
- erforderliche Vorverpackung,
- Beipackzettel und Flyer zur Ware
- Gefahrstoff-Eigenschaften,
- Brandklassen,
- der Füllgrad des Lagers,
- Größe und Gewicht von Verpackungen.
Um nur einige zu nennen.
Wenn im Rahmen eines Wareneingangs der Hinweis erfolgt, dass Stammdaten fehlen, steigern Sie sukzessive Ihre Datenqualität. Oder das Fassungsvermögen eines Behälters oder Fachs wird automatisch angepasst, wenn eine größere Menge als bisher bekannt eingefüllt wird. So wird die Optimierung Ihrer Logistikprozesse zur täglichen Routine.
Papprohre:
Verpackungsmaterial, aber auch Lagerhilfsmittel
2. Optimierung durch organisatorische Ausgliederung des Ersatzteillagers
Wie eingangs erwähnt unterscheiden sich die Anforderungen von Produktions- und Ersatzteillägern deutlich. Ab einer gewissen Mindestgröße sollten Sie dem auch Rechnung tragen. Dann folgt ein eigenständiges Ersatzteillager einer am After Sales orientierten Organisation.
Separierung der Ersatzteil- von den Produktions-Beständen schafft Transparenz
Ab einer bestimmten Größe macht es Sinn, die Produktionsbestände von den Ersatzteilen zu trennen. Natürlich bedeutet das noch mehr Pflege-Aufwand für ohnehin nur mäßig gepflegte Stammdaten. Und auch operativ führt das zu zusätzlich zu buchenden Bestands-Transfers. Allerdings lässt sich einiges davon automatisieren.
Aber letztlich nur können Sie nur so die konkurrierenden Bedarfe trennen. Und dann darauf zielgerichtet durch eine eigene Optimierung der Logistikprozesse reagieren. Immerhin sind die Grundsätze der Disposition für Produktions- und Ersatzteile völlig verschieden. Während Produktionsteile auf konkreten Bedarfen beruhen, nämlich der Vertriebs- und/oder Produktionsplanung, existieren für Ersatzteile fast immer nur historische Verbräuche. Daraus resultieren unterschiedliche Verfahren der Disposition für dasselbe Teil.
Gilt das allgemein und immer?
Nein, natürlich nicht. Nehmen wir zum Beispiel den Anlagenbau mit einmaligem Projektgeschäft. Hier liegt die Wiederhol-Häufigkeit von Teilen meist bei null. Damit lohnt eine parallele Lagerung einfach nicht die zusätzliche Kapitalbindung.
Denn letztlich ist eines klar:
eine Bestandsoptimierung von Ersatzteilen begünstigt immer eine Lageroptimierung
Arbeitszeiten im Ersatzteillager im Rahmen der Optimierung anpassen
Ihr Produktionslager orientiert sich an den Arbeitszeiten der Produktion. Denn das ist deren Kunde. Möglicherweise startet das Lager dann etwas früher, als die Produktion selbst. Oft genug sind die Arbeitszeiten aber auch nur einschichtig, startend um 6 Uhr.
Aber das reicht für ein Ersatzeillager nicht. Nicht nur, dass Kundenaufträge über die gesamte Arbeitszeit der Kunden eintreffen. Das können externe Händler und Endkunden sein, oder eigene Niederlassungen und Service-Techniker. Außerdem schöpfen Sie durch ein frühes Arbeitsende auch noch die Zeit nicht aus, die eine späte Abholung durch Express-Dienstleister ermöglicht. Das kann, je nach Lage im Bundesgebiet, sogar eine Abholzeit nach 21 Uhr sein. Diese ungenutzten Stunden bis zur Cut-Off-Zeit gehen auf Kosten Ihrer Kunden. Denn so kurz können Ihre Durchlaufzeiten im Ersatzteilcenter gar nicht sein.
Die Orientierung der Arbeitszeiten geht jedoch über den einzelnen Tag hinaus. Internationale Kunden erwarten nämlich auch eine Belieferung an Feiertagen. Jedenfalls an solchen, die sie selbst nicht kennen. Webshops und EDI machen die Bestellung möglich.
Warum also nicht liefern?
Gleiches gilt für die rein regionalen Feiertage. Der Hamburger Kunde setzt trotz Allerheiligen auf die Auslieferung Ihrer Ersatzteile. Meist kann an solchen Tagen Ihr Lager mit reduzierter Mannschaft arbeiten. Die Aussagen hierzu liefert eine durchdachte Planung des Personaleinsatzes.
Und dann bleibt da noch der Notdienst. Ein Lager im 3-Schicht-Betrieb tut sich damit naturgemäß leichter, als eines mit nur einer Schicht.
Ergo:
optimalen Kundendienst durch das Ersatzteillager erreichen Sie,
indem Sie Kundenerwartungen übertreffen
3. Lagerung der Ersatzteile optimieren: Wegeminimierung und mehr
In jedem zentralen Ersatzteillager liegen vor allem wenig gängige Teile. Aus Sicht eines Lagers für Fast Moving Consumer Goods (FMCG) sind es eigentlich nur tote Teile. Dadurch und durch die hohe Zahl an Ersatzteilen ergeben sich oft lange Laufwege. Eine Wege-Optimierung durch zielgerichtete Anordnung ist daher unerlässlich. Prinzipiell reicht hierfür eine XYZ-Klassifizierung. Das gilt insbesondere, wenn Sie für tote Teile (kein Verkauf in 12 - 24 Monaten) eine Zusatz-Klasse bilden.
Als weiterer Parameter für eine Optimierung der Logistikprozesse kommt die Anzahl an Lager-Behältern pro Teil hinzu. Denn in der Regel brauchen Sie auch bei gängigen Ersatzteilen nur einen Behälter im Zugriff.
Außerdem sind die physikalischen Eigenschaften zu berücksichtigen
- für sehr schwere Teile kommt Bodenlagerung in Frage,
- sehr lange Teile finden sich in Kragarm-Regalen oder Wannenlagern wieder,
- schwer zu löschende Reifen lagert man besser im Freien
- Gefahrstoffe gehören in Gefahrstoff-Schränke,
- ...
Auf dieser Basis bietet sich als Maßnahme eine Zonierung nach Gängigkeit in Lagerbereichen an. Davon ausgenommen sind Kleinstteile. Denn diese können Sie platzsparend in Schubladen unterbringen. Hinzu kommen Lagerformen, die sehr kompakt die Höhe nutzen, zum Beispiel Lagerlifte.
In Bestands-Immobilien können Sie damit bereits beachtliche logistische Effekte erzielen. Bei einer Neuplanung eines Ersatzteillagers ersetzt dies allerdings eine Lagerplanung nicht.
Im Ersatzteillager die Logistikfunktionen optimieren
4. Mitarbeiter in Lageroptimierung einbeziehen
Alle träumen vom Einsatz von Robotern im Lager. Ganz real wird dies wohl für Ersatzteilläger nie werden. Dafür sind die Aufgaben zu vielfältig, die Wiederholhäufigkeit zu gering. Das verhindert meist die Automatisierung als Teil der Optimierung der Logistikprozesse.
Daher wird der Fokus auf den wichtigsten Leistungsträgern in Ersatzteillägern bestehen bleiben:
auf Ihren Mitarbeitern
Mit Mitarbeitern auf dem Shopfloor die Optimierung der Lagerlogistik gestalten
Wenn Sie eine Tätigkeit tagein, tagaus verrichten werden Sie sie wohl kennen. Sie werden auch wissen, was nicht klappt. Das gilt selbstverständlich auch für Ihre Mitarbeiter.
Darum sind Workshops zur Logistik-Optimierung so wertvoll. Denn oft sind es die kleinen Dinge, die behindern. Diese sind nicht nur meist schnell abstellbar. Eine Behebung der Probleme vermittelt auch das Gefühl, gestalten zu können. Das fördert die Kreativität. Und letztlich bilden auch 1.000 kleine Schritte einen wesentlichen Beitrag auf dem Weg nach vorn.
Allerdings bedarf es dazu der regelmäßigen Übung. Sonst verpufft die psychologische Wirkung schnell. Die allerdings ist wichtig. Denn dadurch identifizieren sich Mitarbeiter auch mehr mit ihrem Arbeitsplatz.
Mitarbeiter-Schulung als integrierter Teil einer Lageroptimierung
Mit jeder Schulung investieren Sie nicht nur in verbesserte Logistikprozesse, in höhere Qualität. Sie investieren auch in Ihre Mitarbeiter. Dabei spielt es keine Rolle, ob die Schulung intern oder extern stattfindet.
Das Schulungsangebot dürfte in Deutschland größer sein, als in den meisten anderen Ländern. Dabei geht es dann auch nicht nur um die (vorgeschriebenen) Klassiker
- Ladungssicherung,
- Zoll,
- Luftfracht,
- Gefahrgut und Gefahrstoff,
- Brandschutz,
- Ersthelfer,
und so weiter. Oft werden diese Schulungen den Mitarbeitern als Aufgabe "verkauft". Damit wird Schulung zur Last.
Diese Einstellung können Sie nur dadurch umgehen, dass Mitarbeiter Schulungen einerseits als Auszeichnung verstehen. Das klappt am besten bei einer Schulung außer Haus. Andererseits können mit einer Schulung auch mehr Verantwortung und ein interessanterer Job verbunden sein. Dann wird ein geschulter Mitarbeiter schnell zur Stütze bei jeder Optimierung der Lagerlogistik.
5. Logistikprozesse optimieren: Kundenorientierung in der Lagerverwaltung
In Ersatzteillägern finden sich deutlich mehr Prozesse, als nur Ein- und Auslagerungen. Eine Optimierung der Lagerprozesse wird nur in kleinsten Lägern manuell sicher gelingen.
Meist steigt mit der Größe der Läger nicht nur die Arbeitsteilung. Auch die Komplexität der Logistikprozesse nimmt zu. Gleiches gilt für die Anforderungen an die Zuverlässigkeit dieser Prozesse. Daher werden im Rahmen einer Lageroptimierung in der Regel auch die Abläufe in der Lagerverwaltung angepasst.
Wegen der Fülle möglicher Prozessoptimierungen eines Ersatzteillagers im LVS können hier nur exemplarisch einige Themen angerissen werden. Sicher werden bei Ihnen auch andere Verbesserungen im Vordergrund stehen. Was das sein kann, bleibt im konkreten Logistikprojekt zu klären.
Bestandssicherheit durch laufende Inventuren
Ersatzteilzentren lagern meist Teile für etliche Maschinengenerationen. Dadurch liegt die Anzahl vorrätiger Artikel oft sehr viel höher als in Produktionslägern. Das treibt den Aufwand für Inventuren. Natürlich können Sie diesen Aufwand auch durch Stichproben-Inventuren reduzieren.
Das alleine garantiert allerdings noch lange keine Bestandssicherheit.
Hier helfen Inventuren im Rahmen des Pick-Vorgangs. Denn oft liegen in Behältern und Fächern nur kleine Mengen. Das vereinfacht eine Zählung. Moderne Lagerverwaltungen unterstützen daher laufende Inventuren durch Maximalmengen pro Fach. Mit nur marginalem Aufwand wird eine Stückzahl 1 oder 2 bestätigt. Oder sogar ein leeres Fach. So gelingt Bestandssicherheit als Teil einer Lageroptimierung quasi nebenbei. Das gilt sogar dann, wenn Sie nur eine Stichprobeninventur durchführen.
Optimierung durch schnelle Rückstandsauflösung bei Fehlteilen
Längst nicht alle Warehouse-Management-Systeme (WMS) sind in der Lage, eine schlanke Rückstandsauflösung umzusetzen. Das ist aber für die Prozessoptimierung der Lagerlogistik unerlässlich. Denn die schlechte Prognostizierbarkeit von oft kleinen Bedarfen führt zwingend zu Fehlteilen.
Manchmal sind aber auch gut gängige Ersatzteile betroffen. Dann wollen Sie sicher alle Rückstände sofort auflösen. Das klappt allerdings nur, wenn hierfür eine Prozess-Optimierung eingerichtet ist. Das beginnt am Wareneingang. Denn nur, wenn dort das Teil als Rückstand identifiziert wird, kann es auf einen Vorzugs-Stellplatz geroutet werden. Sowohl Ware-zum-Mann, wie auch Mann-zur-Ware Logistikprozesse können Sie so optimieren.
Man spricht hier von Cross-Docking oder auch Bypass-Steuerung.
Ersatzteillogistik braucht optimierte Verpackungs-Funktionen
Während Produktionsläger in der Regel an eine Linie oder auf standardisierte Plätze und Wagen liefern, verlassen Ersatzteile immer das Haus. Einzige Ausnahme ist die gleichzeitige Nutzung des Ersatzteillagers durch die eigene Instandhaltung.
Dadurch muss ein Ersatzteil immer verpackt werden. Spätestens beim Export wird daraus sogar eine zwingende Vorschrift. Denn dann müssen die Mengen eines Ersatzteils pro Colli in den Zoll-Dokumenten genannt werden. Das geht auch manuell, ist aber hochgradig fehleranfällig.
Daher umfasst die Prozessoptimierung in der Ersatzteillogistik auch das Verpacken im Prozess-Fluss. Und wie bei allen Logistik-Optimierungen sind gute Stammdaten eine wichtige Voraussetzung. Denn erst mit einer geführten Auswahl des Verpackungsmaterials garantieren Sie eine hohe Qualität. Außerdem können Sie die hinterlegten Gewichte der Verpackungen für eine Inhaltskontrolle nutzten. Denn nur so können Sie das theoretische Gewicht eines Packstücks mit dem gemessenen Wert vergleichen.
Analyse der Anzahl von Auftragspositionen im Rahmen der Prozessoptimierung im Ersatzteillager
Eine zusätzliche Stufe der Optimierung Ihres Ersatzteillagers erreichen Sie durch "Pick-und-Pack". Weil oft nur einzelne Positionen bestellt werden, lohnt die Kombination von Picken und Packen in einen einzigen Prozess-Schritt. Der Verzicht auf den Wechsel von Transaktionen begünstigt diesen schlanken Ablauf.
Im Bild oben sehen Sie die zugrunde liegende Analyse: 57 % aller Aufträge bestehen nur aus einer einzigen Position. Also eine typische Techniker-Belieferung.
Warum wollten Sie hier auf eine maximal schlanke Buchungsfolge verzichten?
Es versteht sich von selbst, dass die Übertragung dieser Verpackungs-Daten in Richtung
- Zoll-System
- Fracht-System
nicht nur Prozess-Qualität garantieren, sondern auch die Arbeit der Weiterverarbeitung vereinfachen.
Interne Benachschubung und Kommissionierstrategien
Ein weiterer Hebel zur Optimierung des Lagers durch Nutzung von WMS-Funktionen liegt in den unterschiedlichen Auftragsmengen. In der Analyse unten ist zu sehen, wie oft bestimmte Mengen verkauft werden. Ersatzteile werden häufig sowohl mit der Stückzahl 1 wie auch in großen Mengen verkauft. Dann muss sich die Kommissionierung daran ausrichten. Hierfür sorgen hierarchisch greifende Kommissionierstrategien. Große Auftragsmengen werden dann zum Beispiel von Paletten gepickt. Eine Auftragsposition mit Stückzahl 1 pickt sich allerdings wesentlich schneller aus einem Greifregal.
Eng damit verknüpft ist eine interne Benachschubung. Dadurch liegt immer genug im manuell bedienten Greifregal.
Analyse der Auftragsmengen Ersatzteile für Lageroptimierung
6. Lösungen außerhalb von ERP und Lagerverwaltungssystem (LVS) nutzen
Gerade die fortschreitende Digitalisierung bietet zusätzliche Chancen zur Lageroptimierung. Denken wir an die Wegezeiten der Mitarbeiter. Immerhin handelt es sich meist um deren höchsten Zeit-Verbrauch. Hier bieten die wenigsten Lagerverwaltungen Optimierungs-Algorithmen.
Daher kann für diesen Zweck die Anbindung spezialisierter Software merkliche Effekte bieten. Als Beispiel für eine Software, die durch intelligente Pick-Aufträge Wegezeiten minimiert, kann Lucas Engage dienen. Entscheidend für die Auswahl einer zusätzlichen Software sind hierbei die einfache Implementierung und die zu erwartenden Effekte.
Download Whitepaper zur Optimierung von Ersatzteillägern
Sie können diesen Beitrag über Ersatzteillogistik hier als pdf herunterladen:
sofortiger Download
ohne Ihre Daten
Sie wollen die Optimierung Ihres Ersatzteillagers angehen?
Der geübte Blick von außen hilft Ihnen dabei.
Warum also nehmen Sie nun nicht einfach unverbindlich und kostenlos Kontakt zu mir auf?
Denn durch Logistikberatung gepaart mit viel Erfahrung im Maschinenbau kann ich Sie bei der Einführung von Lager-Prozessen und deren Optimierung Ihrer Lager-Struktur unterstützen.
andreas.noll@no-stop.de
Laden Sie hier die Übersicht über meine
Projekte zur Ersatzteillogistik herunter
sofortiger Download
ohne Ihre Daten