Automatisierung durch “Ware zum Mann”: Wartezeiten vermeiden
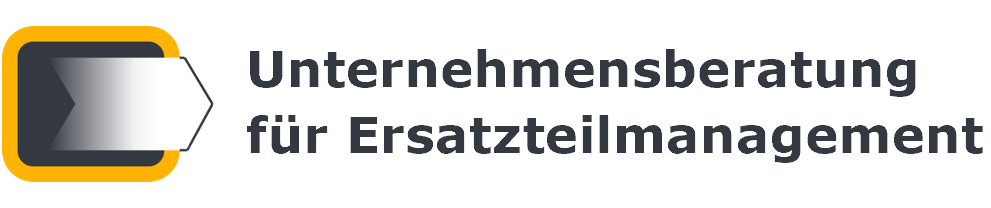
Automatische Kleinteilelager (AKL) sind häufig nur zu Beginn ihres Betriebs effizient. Spätestens, wenn Mitarbeiter auf Picks warten müssen, ist es Zeit für eine Prüfung der technischen Prozesse. Oft sind dabei mehrere EDV-Systeme involviert. Dadurch steigt die Komplexität. Das macht Optimierungen bei allen Ware zum Mann Anlagen so unbeliebt.
Wartezeit kostet. Erst recht bei Ware zum Mann
Automatische Kleinteilelager (AKL) sind schnell. Und trotzdem finden sich immer wieder Anlagen, die Mitarbeiter zum Warten zwingen.
Doch diese Wartezeit muss nicht sein.
Denn eine konsequente Ausrichtung der IT an schnellen Abläufen bringt unerwartete Reserven zum Vorschein.
Kommissionier-Prozesse am AKL lassen sich optimieren
Wie kann das sein, wo doch die Ware zum Mann Kommissionierung eigentlich effizient ist?
Wie die folgende Grafik zeigt, verstecken sich die Reserven allerdings häufig. In der Summe sind sie jedoch deutlich größer, als man erwarten würde:
Ware zum Mann Kommissionierung birgt Potenzial mit riesigen Reserven
In diesem Fall macht der Leistungsverlust durch Stillstand der Regalbediengeräte (RBG) sogar 1.000 Positionen aus.
Genau diese spüren Ihre Mitarbeiter:
"das Gerät steht, und ich habe nichts zu tun"
Die Ursachen hierfür sind meist vielfältig. Daher kann hier nur ein Überblick beschrieben werden. Auch das Herangehen, um bei Ihnen die Potenziale zu heben, unterscheidet sich von anderen Anlagen.
Effizienz der Anlage beurteilen
Vorhandene Datenbanken nutzen
Im Normalfall werden Mann zur Ware Anlagen über einen Materialflussrechner gesteuert. Damit können Sie Daten aus der dazugehörigen Datenbank auslesen. Im Normalfall, und nur als ein Element eines Verbesserungsprojekts. Solche Datensätze sind mit eigentlich immer Zeitstempeln versehen. Mithilfe dieser Informationen können Sie
- Aufträge,
- die Anlage,
- Ein-, Aus- und Umlagerungen
bestimmen. Auch die Versorgung von Arbeitsplätzen am AKL mit Behältern lässt sich so ermitteln.
Besonders interessant sind diese Daten natürlich zu Ihren Spitzenzeiten. Der Erfolg eines Optimierungsprojekts lässt sich auch nur in diesen Zeiten sinnvoll ermitteln.
In einem Ersatzteillager sind das meist die Zeiten zwischen 14:00 und 17:00 Uhr. Eine durchschnittliche Leistung hilft Ihnen nämlich wenig. Da zudem nicht jeden Tag und nicht zu jeder Zeit die maximale Leistung abgefragt wird, ist eine spezialisierte Analyse unumgänglich.
Anlage beobachten
Die zweite Komponente zur Beurteilung einer Anlage besteht in einer konsequenten Beobachtung ihrer Abläufe. Oft lassen sich mit bloßem Auge Wartezeiten des Automatischen Kleinteilelagers (AKL) feststellen. Es kommt sogar vor, dass explizit Wartezeiten in Abläufe einprogrammiert wurden. Aber auch ungleich gefüllte Gassen führen zur Überlast einer einzelnen Gasse. Dann stehen gleichzeitig die anderen Regalbediengeräte still. Dies kann sogar bei gleich gefüllten Gassen passieren. Nämlich dann, wenn Behälter mit hochgängigen Ersatzteilen in einer Gasse konzentriert sind. Solche Ungleich-Verteilungen sind ganz häufig offen sichtlich.
Spielzeiten aufnehmen
Die verfeinerte Methode der Anlagen-Beobachtung besteht in einer Zeitaufnahme. Damit sind nicht etwa Ihre Mitarbeiter gemeint. Vielmehr geht es um die automatisierte Anlage. Eine solche Zeitaufnahme sollte jedoch erst in einem fortgeschrittenen Projektstadium erfolgen. Ein gern gewähltes Mittel stellt hierbei die Video-Aufnahme dar. Über eine Videoschnitt-Software können Sie komplexe Bewegungen zerteilen. Mit hinreichender Genauigkeit erlaubt Ihnen die Software dann, einzelne Elemente eines Spiels zeitlich bewerten.
Darüber hinaus sehen Sie Blindleistungen: Bewegungen, die nicht unmittelbar zu Ein- und Auslagerungen beitragen.
Nach Gängigkeit der Ersatzteile einlagern
Wie bei jedem manuellen Lager erlaubt die Wahl der Einlagerungsstrategie auch bei Ware zum Mann Anlagen eine Wege-Optimierung.
Weniger Fahrzeit lässt sich übersetzen in Mehr Picks.
Allerdings gestaltet sich die Definition der Einlagerungsstrategien deutlich komplexer. Erst recht bei mehrfach tiefen Fächern. Oder, wenn Sie auch Leerbehälter im AKL speichern.
Solche Einlagerungsstrategien können sie extern festlegen. Zum Beispiel durch die Ziel-Gängigkeit eines Fachs im Sinne einer XYZ-Klasse. Mit jedem Behälter führen Sie dann ebenfalls eine Gängigkeitsklasse.
Das stimmt allerdings nur in der ersten Näherung. Denn eigentlich greifen Sie nur selten auf mehr als einen Behälter zu. Dann stehen mehrere Behälter desselben Ersatzteils im Weg.
Aber auch ohne eine externe Festlegung von Klassifizierungen kann ein Materialflussrechner Gängigkeiten von Behältern ermitteln. Die Zeit seit der letzten Auslagerung für eine Entnahme gibt einen guten Maßstab. Per Definition sind aus dem Wareneingang eingelagerte Behälter gängig.
Gassen gleichmäßig belegen
Ziel einer optimierten Belegung muss es sein, alle Regalbediengeräte bei der Auslagerung gleich zu belasten. Dazu gilt es, bei der Einlagerung alle Gassen zum gleichen Füllgrad zu bringen. Der gleiche Füllgrad betrifft speziell auch die gängigen Artikel. Diese werden bei einer XYZ-Klassifizierung oft mit X gekennzeichnet. Sonst bewegt sich in Spitzenzeiten nur ein Gerät. Alle anderen müssen warten. Und natürlich damit auch Ihre Mitarbeiter.
Solche pauschalen Aussagen gelten für identisch gestaltete Gassen. Unterscheiden sich einzelne Ihrer Gassen technisch, so sollen trotzdem alle Regalbediengeräte bei der Auslagerung gleich belastet werden. Das hat Konsequenzen auf die zielgerichtete Einlagerung.
Ein weiterer Spezialfall betrifft hochgängige Ersatzteile. Für diese kann eine verteilte Lagerung in mehreren Gassen Sinn machen. Effekte werden sich allerdings nicht immer zeigen. Die Effekte werden nur messbar, wenn für diese hoch gängigen Teile die Auslagerung aus mehreren Behältern gleichzeitig erfolgen darf. Die Anwendung eines strengen FiFo stände dieser Philosophie im Weg.
Gerade bei extrem gängigen Ersatzteilen geht es allerdings auch ganz anders: diese Artikel lagern am Pickplatz und werden weder ein- noch ausgelagert.
Mehrfach tiefe Fächer
= gesteigerte Komplexität
Eine deutliche Steigerung der Komplexität verursachen Fächer, die mehr als nur einen Behälter hintereinander lagern können. Dies geht meist einher mit Aufnahme-Gabeln, die ebenfalls mehrere Behälter aufnehmen können. Eine Wege-Optimierung umfasst in solchen Fällen auch die Umlagerungen. Ob es sich tatsächlich lohnt, komplexe Umlager-Spiele durchzuführen, zeigen Simulationen. In diesen Fällen kommen Sie ohne detaillierte Zeitaufnahmen nicht aus.
Nachts Anlage automatisiert reorganisieren
Um Ihr AKL in den Zielzustand für eine Wege-Optimierung zu bringen, bieten sich die Last-armen Zeiten an. Dies wird in der Regel die Nacht sein. Außerdem natürlich am Wochenende.
Wenn Reorganisationsläufe zeitgesteuert beginnen und enden, müssen Sie eines berücksichtigen:
die Bearbeitung von Aufträgen zur Reorganisation in größeren Batches kann durchaus bis in die folgende Arbeitszeit dauern.
Auch das würde Mitarbeiter behindern.
Ein sehr hoher Füllgrad ist übrigens auch eine gute Möglichkeit, die Effizienz eines AKL zu minimieren. Die Methode Ware zum Mann trifft dann im Mittel auf lange Wege. Gleichzeitig werden Reorganisationsläufe deutlich verlangsamt. Denn jetzt benötigen Ihre Regalbediengeräte ebenfalls lange Wege. Durch eine Auslagerung von Lagerleichen können Sie dann allerdings Abhilfe schaffen.
Die Erfahrung zeigt, dass durch Reorganisation selbst Automatische Kleinteilelager mit 100.000 Behältern binnen weniger Tagen eine fühlbare Steigerung der Leistung erfahren. Eine detaillierte Messung ergab bis zu 10% zusätzlicher Auslager-Leistung.
Ohne eine gute Auslagerstrategie verschenken Sie Effizienz
Lassen Sie die Statistik für Sie arbeiten. Je mehr Aufträge gleichzeitig in Bearbeitung sind, desto eher kann Ihr Materialflussrechner Wartezeiten vermeiden. Das geht allerdings zu Lasten der Durchlaufzeit. Im Expressgeschäft ein kostbares Gut. Hier hilft nur Fingerspitzengefühl bei den Einstellungen. Und eine Strategie, die die maximale Verweildauer eines Auftrags im Materialflussrechner begrenzt.
Es gibt eine Reihe von Möglichkeiten, effektiv auszulagern.
Gar nicht erst auszulagern ist die eine. Wenn nämlich ein Behälter von mehreren Arbeitsplätzen angefordert wird, warum wollen Sie ihn überhaupt wieder einlagern? Nur, um ihn sofort wieder auszulagern? Gerade bei Rückstandsauflösung für Fehlteile kann hier die Lieferperformance oft deutlich gesteigert werden. Sinnvoll ist dafür eine Fördertechnik, die als Endlosschleife alle Kommissionierplätze verbindet. Das ermöglicht eine beschleunigte Abarbeitung solcher Ersatzteil-Aufträge.
Das optimierbare Volumen für Auslagerungen hängt unmittelbar von der Zahl gleichzeitig in Bearbeitung befindlicher Lieferungen oder Teilaufträge ab. Mit Put-to-Light Systemen können Sie in der Kommissionierung fehlerarm etliche Aufträge gleichzeitig abarbeiten.
Eine weitere Variante, um dem Materialflussrechner Optimierungen in der Abarbeitung zu ermöglichen, ist die Verlängerung der Staustrecken vor den Arbeitsplätzen. Je nach räumlichen Gegebenheiten kann dies auch die gleichzeitige Nutzung von 2 parallelen Staustrecken sein.
Eigentlich selbstverständlich, aber doch nicht immer umgesetzt, ist eine frei wählbare Reihenfolge der Auftragspositionen. Wird die Reihenfolge der Auftragspositionen extern vorgegeben, sinkt der Spielraum für optimierte Zugriffe bei der Auslagerung fast auf die Zahl der Arbeitsplätze.
Wie wird Ihr Materialflussrechner beauftragt?
Auch die Beauftragung Ihres Materialflussrechners durch die Lagerverwaltung spielt eine Rolle.
Sie kennen Tetris?
Ihre Lagerverwaltung auch?
Hier ist gemeint, dass Ihr Warehouse Management System aus einem Pool auszulagernder Aufträge zunächst solche übergibt, die auf Lücken in der Warteschlange vor dem AKL trifft. Natürlich setzt dies voraus, dass Ihr Lagerverwaltungssystem zumindest die Gassen kennt, aus denen auszulagern ist.
Mitarbeiter an Ware-zum-Mann Anlagen müssen mitspielen
Was passiert, wenn ein Mitarbeiter seinen Arbeitsplatz am AKL verlässt?
Ohne eine Abarbeitung noch offener Aufträge bleibt die Warteschlange für diesen Kommissionierplatz bestehen. Es kommt vor, dass sich in dieser Warteschlange ein Ersatzteil befindet, das auch an einem anderen Arbeitsplatz benötigt wird. Über kurz oder lang kann dieser andere Arbeitsplatz nicht mehr bedient werden. Eine virtuelle Warteschlange ließe sich durch eine komplexe Strategie auflösen. Allerdings versagt die beste Strategie, wenn sich das Teil, oder besser der Behälter für dieses Teil, auf einer Staubahn befindet.
Darum müssen Kommissionierplätze, an denen nicht mehr gearbeitet wird, vorher leergefahren werden.
In Spitzenzeiten Wareneingänge drosseln
Rein organisatorischer Natur ist der Verzicht auf Wareneingänge in Spitzenzeiten. Ohne Wareneingang keine Ressourcen-Nutzung. Lediglich (Ersatz-)Teile mit Unterdeckung genießen Priorität. Es sei denn, sie werden über reine Cross-Docking Prozesse manuell abgewickelt.
Pick-und-Pack steigert Arbeitsinhalte
Nicht immer ist die Mitarbeiter-Kapazität der Ware zum Mann Kommissionierung der Engpass im Lager. Dann lassen sich zur Vermeidung von Wartezeiten auch Arbeitsinhalte ausweiten. So wird die kostbare Ressource Zeit nicht vergeudet.
Die Reduzierung der Arbeitsteilung ist hierfür ein gängiger Ansatz. Wird am Kommissionierplatz auch gleich verpackt, reduziert sich meist auch die Durchlaufzeit im Ersatzteillager.
Erfolg von Maßnahmen messen
In diesem Beitrag haben Sie einige Möglichkeiten gesehen, wie man die Ware zum Mann Kommissionierung verbessern kann. Es macht wenig Sinn, gleichzeitig viele Maßnahmen umzusetzen. So wäre auch der Erfolg jeder einzelnen Maßnahme kaum nachvollziehbar. Das "Feintuning", das zu den meisten Maßnahmen dazugehört, wäre außerdem erschwert. Damit würden Sie kaum die nachvollziehbaren Wirkungen erzielen, weil gleichzeitig an mehreren Stellschrauben gedreht wird.
Unten nun ein reales Beispiel für ein Optimierungsprojekt. Die erzielte Leistungssteigerung war beachtlich. Häufig jedoch erst nach mehreren Optimierungsrunden für einzelne Teilprojekte:
Download Whitepaper zur Optimierung Ware zum Mann
Sie können diesen Beitrag zur Kommissionierung Ware-zum-Mann hier als pdf herunterladen:
sofortiger Download
ohne Ihre Daten
Ihre Mitarbeiter dürfen nicht auf Ihre Fördertechnik warten
Nutzen Sie daher meine Expertise aus Optimierungsprojekten
Warum nehmen Sie nicht einfach unverbindlich und kostenlos Kontakt zu mir auf?
Denn als erfahrener Logistik Consultant kann ich Sie bei der Einführung schneller Lager-Prozesse und bei deren Optimierung unterstützen.
Andreas.Noll@no-stop.de