Ersatzteilverfügbarkeit steigern: nur mehr Bestand reicht nicht
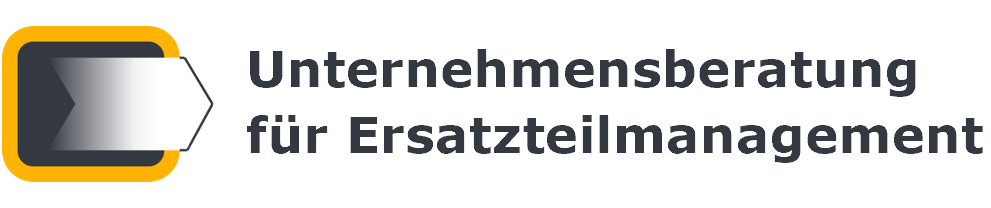
Eine ausgezeichnete Lieferfähigkeit von Ersatzteilen bindet Kunden im After Sales. Das setzt allerdings eine hohe Ersatzteilverfügbarkeit voraus. Die sollte deshalb unabhängig von Teile-Bedarfen für die Produktion sein. Denn sonst verhindert die Bedarfskonkurrenz um Teile nicht nur Transparenz. Die kostet außerdem intern Personal und Nerven.
Klar ist aber auch:
dabei gewinnt in der Regel die Produktion
Schon, weil es sich um deren geplante Bedarfe handelt. Und auch Lieferanten als verlängerte Werkbank werden oft und unnötigerweise in Anspruch genommen.
Doch warum sollte Ihre Ersatzteilverfügbarkeit darunter leiden?
Strukturänderungen, damit Detail-Optimierungen kein Stückwerk bleiben
Einer mäßigen Teile-Verfügbarkeit begegnen nicht wenige Anbieter mit Termin-Jägern. Es soll sogar passieren, dass Komponenten aus der laufenden Montage ausgebaut werden.
Doch das können keine ernst zu nehmenden Lösungen sein. So lange Produktion und After Sales Service auf den gleichen Bestand zugreifen, so lange wird eine Bedarfskonkurrenz bestehen.
Diesen Streit um zu geringe Bestände an einzelnen Teilen können Sie allerdings nicht pauschal durch eine Erhöhung des Bestands erledigen. Denn die Arbeitsweisen von Produktions- und Ersatzteil-Disposition unterscheiden sich grundlegend. Da hilft es wenig, einfach nur den Druck auf die Disponenten zu erhöhen. Schließlich können Sie ein Einzelteil entweder auf Basis einer Vertriebs- und Produktionsplanung disponieren.
Oder aber, Sie nutzen Vergangenheitswerte für die Ersatzteil-Bedarfe. Nur eben kaum beides gleichzeitig.
Aus diesem Dilemma gibt es einen Ausweg: Die Implementierung eines eigenständigen Ersatzteillagers. Denn dann sind die Bedarfe sauber voneinander getrennt. Was bleibt sind Benachschubungen des Ersatzteillagers aus dem Produktionslager. Wann diese durch das Produktionslager befriedigt werden, kann in einem eigenständigen SLA (Service-Level Agreement) vereinbart werden.
Doch zunächst ein Schritt zurück:
Fokus auf die Ersatzteilverfügbarkeit: aber warum eigentlich?
Kunden verlangen nach ununterbrochener Maschinenlaufzeit. Schon Wartungen sind deshalb unerwünscht und müssen oft in der Nacht oder am Wochenende stattfinden. Unerwartete Reparaturen stellen erst recht eine massive Störung der Produktion dar.
Und deshalb lässt sich nur durch eine hohe Verfügbarkeit Ihrer Ersatzteile diese Stillstandszeit minimieren.
Daher entsteht bei Reparaturen schnell ein hoher Druck auf jeden Ersatzteil-Lieferanten. Ebenso, wie die Erwartung einer sofortigen Verfügbarkeit. Dabei lassen wir die juristischen Anforderungen an die Ersatzteilverfügbarkeit hier bewusst außen vor.
Bedarfskonkurrenz von Sekundärbedarfen aus Fertigung entflechten
Etliche Unternehmen versorgen den Ersatzteilmarkt aus dem Produktionslager. Die Kern-Idee eines einzigen Lagers sowohl für Ersatzteile wie auch Produktions-Komponenten ist einfach:
Bei unregelmäßigen Bedarfen erlaubt eine gemeinsame Verbrauchsstatistik häufiger den Griff in ein gefülltes Lagerfach. Außerdem kommen operative Überlegungen hinzu, wie
- in der Aufbau-Organisation eine einzige Lager-Organisation,
- keine internen Umlagerungen von einem ins andere Lager,
- nur einmal die Pflege von Stammdaten,
- lediglich eine Teile-Disposition.
Solche Überlegungen wiegen um so gewichtiger, je kleiner die Seriengröße der Maschinen und Anlage ist.
Teile-Disposition für Produktionsbedarfe
Die meisten Serien-Fertiger planen ihren Vertrieb Monate im voraus. Aus diesem Vertriebsplan wird dann ein Produktionsplan abgeleitet. Aus diesem erzeugt der MRP anschließend Planbedarfe für Komponenten. Um die Lieferzeit der Komponenten zu berücksichtigen, benutzt die Disposition damit die Bedarfe, die oft Monate in der Zukunft liegen. Außerdem wird die Ungenauigkeit zwischen Plan und vertrieblicher Wirklichkeit durch Sicherheitsbestände abgebildet. Alle diese Informationen finden sich sichtbar auf der Zeitachse des ERP wieder.
Lediglich für C-Teile arbeitet auch die Produktion oft mit Vergangenheitswerten. Und sei es nur, dass die Kanban-Behälter auf der Basis der Vergangenheit ausgelegt werden.
Ersatzteil-Disposition arbeitet meist mit historischen Bedarfen
Reparaturen kündigen sich nur selten an. Das werden auch Verfahren mit dem Term Predictive nur wenig ändern.
Wenig wissenschaftlich ausgedrückt lautet das Motto:
es wird ungefähr so weitergehen wie bisher
Diese Methode erzwingt Sicherheitsbestände. Auch und gerade für Ersatzteile, die nur selten gehen. Denn kein Kunde will warten (s.o.). Als Maß für die Verlässlichkeit der Fortschreibung der Vergangenheit gelten
- Gängigkeit
- Ersetzungen und der Lebenszyklus
- ggf. die Maschinenpopulation
und
- Mengen-Variation.
Reparatur-Bedarf im Vergleich mit Bedarf für Fertigungsaufträge
Die Idee einer Verfügbarkeitsprüfung entspringt einer Momentbetrachtung:
Ist zum Zeitpunkt des Kundenbedarfs
für Ersatzteile genug frei verfügbarer Bestand vorhanden?
Denn nur bei Ersatzteilverfügbarkeit können Sie dem Kunden einen Liefertermin nennen. Doch das ist nur die halbe Wahrheit. Denn der Sekundär-Bedarf für Fertigungsaufträge liegt möglicherweise in naher Zukunft. Zum Zeitpunkt Ihrer Prüfung ist der Bestand zwar für die Fertigung geplant. Doch ohne Freigabe des Fertigungsauftrags ist ein solcher Bestand in der Regel noch frei verfügbar.
Also erfolgt eine manuelle Prüfung, ob dieser Bestand entnommen werden darf. Sonst winkt die Verschiebung des Fertigungsauftrags. Dieser Bedarfskonflikt lässt sich nur durch immer ausreichenden Bestand lösen. Jetzt ist "nur noch" zu definieren, was ausreichender Bestand sein könnte.
Sie mögen ahnen:
die Verfahren der Ersatzteil-Disposition und der Produktions-Disposition passen nur sehr bedingt zusammen
Das hat Auswirkungen beim Abgleich von Beständen und Bedarfen. Und um die negativen Effekte zu reduzieren, kann es Sinn machen, das Ersatzteillager separat aufzustellen. Das vereinfacht auch den Einsatz der Ersatzteil-Prognose. Denn nun lassen sich geplante Nachfrage und reale Kundenaufträge konkret in der Bestandsprognose abbilden.
Ersatzteilverfügbarkeit wird verfälscht durch geplante Wartung
Die Bedarfskonkurrenz für Ersatzteile kann aber auch innerhalb eines Ersatzteillagers auftreten. Das gilt nicht nur für zeitgleich eintreffende Kundenaufträge. Denn bei Aufträgen auf Termin kann sie ebenfalls auftreten. Den Klassiker stellen geplante Wartungen dar. Weil sich die Termine bei vernünftiger Planung absehen lassen, können Händler und Niederlassungen mit Vorlauf bestellen. Von Ersatzteillägern sind solche Aufträge zur Bereitstellung mit Vorlauf gern gesehen. Denn dadurch können sie Auftragslücken füllen. Das verstetigt damit die Personalplanung.
Wartungskits ermöglichen Zusatz-Bestände
Durch das Bilden von Kits kann das Ersatzteilmanagement Bestand aufbauen. Dieser Bestand ist entkoppelt von ad-hoc-Bedarfen für Reparaturen. Das gilt selbst dann, wenn es um die gleichen Teile geht. Denn durch die Nutzung eigenständiger Artikelnummern für die Kits besteht nur implizit ein zusätzlicher Bestand der Komponenten. Das muss man allerdings wissen.
Tatsächlich soll es jedoch schon vorgekommen sein, dass Kits demontiert wurden. Dann nämlich, wenn ganz dringend eine der Komponenten benötigt wurden.
Im Übrigen muss die Bildung von Kits natürlich nicht nur auf die Wartung beschränkt bleiben. Die gleiche Logik gilt für häufig auftretende Reparaturen oder Feld-Aktionen.
Bei allen Kits gilt aber auch:
Fertigungsaufträge für Wartungskits erzeugen Bedarfe. Und diese treten in Konkurrenz mit ad-hoc-Bedarfen für Kundenaufträge. Jetzt lassen sich die Prioritäten aber im Rahmen des Ersatzteilmanagements klären. Und zwar intern.
Manuell verwaltete Sonder-Bestände vermeiden
An dieser Stelle noch eine Erinnerung:
oft soll als Ausweg aus dem aufgezeigten Dilemma der Bedarfskonkurrenz ein Sonderbestand herhalten.
Für besonders oft betroffene Artikel legt "jemand" eine Liste an. Hierfür wird dann ein Sonderbestand aufgebaut. Allerdings verfolgt später kaum "jemand", ob regelmäßig nachbestellt wird. Und auch die Zahlenbasis wird in der Folge nicht mehr hinterfragt. So kommt es, dass sukzessive wieder Fehlteile auftauchen. Dafür liegen andere Sonderbestände wie Blei an Lager: Lagerleichen. Damit drohen Wertberichtigungen. Nach einer Weile vergessen die Disponenten im Tagesgeschäft, dass es diese Liste überhaupt gibt. Schließlich ist sie im System nicht sauber abgebildet.
Womit das Kernproblem angesprochen ist. Alles, was nicht im ERP-System ermittelt und in Stammdaten umgesetzt wird, altert nicht nur. Die Pflege wird irgendwann vernachlässigt. Das liegt daran, dass "jemand" eben doch nicht in dieser Firma Verantwortung trägt.
Download Whitepaper zur Steigerung der Ersatzteil-Verfügbarkeit
Sie können diesen Beitrag zur Trennung von Produktions- und Ersatzteilbeständen hier als pdf herunterladen:
sofortiger Download
ohne Ihre Daten
Sie wollen Ihre After Sales Kunden durch eine hohe Ersatzteilverfügbarkeit binden?
Dann kann die Trennung der Ersatzteil-Bedarfe von den Produktionsbedarfen ein Ansatz sein.
Warum also nehmen Sie nun nicht einfach unverbindlich und kostenlos Kontakt zu mir auf?
Denn als erfahrener Unternehmensberater für den Mittelstand kann ich Sie bei der Einführung von Planungsprozessen für Ersatzteile und der Bestands-Optimierung unterstützen.
andreas.noll@no-stop.de
Laden Sie hier die Übersicht über meine
Projekte zur Ersatzteillogistik herunter
sofortiger Download
ohne Ihre Daten